

- #Computerized maintenance management system sap driver
- #Computerized maintenance management system sap manual
In the following example tells you where the usage of Field Instrumentation Maintenance System (FIMS) had became the part of the daily routine.
#Computerized maintenance management system sap manual
Control valve related manual andĪutomatic work orders in Delayed Cooker unit This information is unique and essential to make on-time decisions in order to avoid slow-downs or shut-downs (see Pic 2). Reading other parameters such as drive-signal (or drive current), supply pressure and cycle-count, they are able to have information that helps troubleshoot and prevent problems. Also, reading the set-point and the current travel of control valves by accessing information in the valve positioners, they are able to know the status of the valve's condition. This is critical in order to avoid slow-downs or a shut-down of production. Examples: by reading the cell temperature of a pressure transmitter, they check the impulse-line heaters. The frame applications and DTMs support the preventive maintenance strategy with self-diagnostic and condition monitoring. This information is available from a safe and secure location which reduces the number of trips into the production area and provides faster response to potential problems.
#Computerized maintenance management system sap driver
Using a combination of the device DTM (similar to a device driver that is included with a new printer) and the PRM device management tool (examples of a frame application), it is able to: diagnose problems with smart devices, perform loop checks, modify the configuration and get a visual overview (range, alarms, etc.) of the device. The maintenance staff, including engineers and technicians benefit from having quick access to information that provides early warning of potential problems. In the 15 key production units, there are 3,855 instruments connected to the computerized maintenance management system (CMMS). Devices at the Danube refinery are connected to an on-line system using both HART and FOUNDATION™ fieldbus field digital communication technology- many of these having DTMs (see Pic 1.) that provide simple and fast information access which is traceable-documenting device status and changes. In Hungary the MOL production sites currently have about 30,000 smart devices the majority installed at the Danube location. Using the wealth of the available information, its goal was to improve maintenance processes, and human competencies and skills. PRM from Yokogawa enabling fast, simple and safe device configuration and diagnostics as an important part of their on-line maintenance system strategy.īy using PRM, it supports the field instrumentation maintenance activity providing information used to identify the location of an asset problem, for device repair, and remotely accessing device information and changing the device configuration. The on-line systems use FDT technology embedded in their device configuration and maintenance systems. This Danube Refinery set-out to improve their operation and decided to overhaul its maintenance systems with a new, united asset management system strategy. The Danube refinery is a complex refinery with deep conversion units, allowing the high yield of motor fuels and other valuable products from heavy and sour crudes. Its crude distillation capacity is 8.1 mtpa and complexity ratio is 10.6 (NCI). The Refinery is located in Százhalombatta, close to Budapest. The Danube Refinery has been the only Hungarian MOL refinery to conduct crude distillation since 2001.
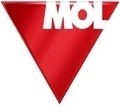
All businesses are supported by cutting edge supply-chain optimization. MOL Group is the only refiner of petroleum products in Hungary, Slovakia and Croatia. The company top priorities also include compliance with the latest environmental regulations and major projects aim at improving environmental cleanliness and product quality. MOL's strategic aim is to further developing all its refineries, increasing the ratio of top quality motor fuel products and exploiting all the opportunities for organic growth on the basis of its excellent downstream knowledge. MOL -Group's Downstream Division operates 6 production units with a total capacity of 20.9 mtpa renfing and 2.1 mtpa petrochemicals with more than 1700 service stations under 8 brands in 11 Central European countries, all supported by a far-reaching logistics system and driven by Supply Chain Management.
